Problems and Countermeasures at GE Appliances and Herman Miller:
- Problem 1: Clarify what is the problem to solve
- Problem 2: Ensure each member is coming to work healthy
- Problem 3: Make assembly line work safe for social distancing
- Problem 4: Maintain social distance for Team Leader Andon response
- Problem 5: Apply social distancing to other, non-assembly line, work areas
- Problem 6: Resolve the many other safety concerns that are cropping up
- Cleaning surfaces
- Cleaning air – Ventilation
- PPE
- Incidental contact, incl water fountains, restrooms, hand sanitation stations
- Regulatory and other
Problem One: Clarify what is the problem to solve
GEA: Appliances are considered essential infrastructure, so GEA is allowed to operate. People need refrigerators and to be able to wash clothes, etc.
HM: Production for contract orders from general industry has ceased while continuing to fulfill critical orders for healthcare and government, including PPE for area (western Michigan) hospitals.
- Question: How to run production under the challenges presented by the need for social distancing?
- Thinking: Consider lean thinking principles to redesign of work in light of the concerns, constraints, and challenges presented by the coronavirus and social distancing?
- Approach: Redesign work so production can proceed safely for all members.
Problem Two: Ensure each member is coming to work healthy
- Question: How to ensure no one sick comes to work?
- Thinking: Safety is the always first concern.
- Approach: Implement a preventive measure – jidoka or pokayoke – to prevent a sick person from entering the plants.
GEA
Initially tried to run production as usual, but with the concerns of social distancing, decided to stop, assess the situation, and devise a strategy.
The first order of business: can’t have sick people coming to work. So concluded that mass temperature testing is the right countermeasure.
Problem breakdown – technical: GE Appliance Park has MANY entrances, as well as multiple locations of operations. Many people enter through turnstiles within a short time.
Problem breakdown – social: VP operations was concerned that the plant team was struggling with the problem – throwing solutions at it – and needed help with some lean problem-solving and challenged the lean team to help.
So, the team stepped back to grasp the current conditions:
- How many people enter the facility?
- What would the TT be? The team calculated a rough estimate of 4 seconds.
- The initial response of the staff was, “That’s impossible!” Rich responded by coaching: “Well, that’s the TT. We have a gap between the TT and c/t. The question to address is, what do we need to do?”
Other considerations: People don’t arrive at the same time – perhaps 500 within about 30 minutes, then not many – a bottleneck problem, no heijunka, with constraint within a certain times.
The problem-solving process: The original method of taking temp – a thermometer held in place within 1-inch of forehead…they configured a contraption with the thermometer and sensors on a pole – an awful solution.
So Rich challenged the team to come up with something better. They found a thermal camera (probably similar to those used in airports) for $5,000.
They decided to try it, setting the thermal camera on a tripod with bright orange legs about 3-4 feet away from the entrance, and marking 6-foot social distancing on the floor for employees waiting in the queue. An individual only has to come within 3-4 feet for the reading. The camera was set to check for the Centers for Disease Control and Prevention’s (CDC) temperature standard of 100.4 degrees. The resulting cycle time was 6 seconds, still two seconds away from the goal, but getting close.
Upon performing R&R to check its reliability, the team decided the system worked and seemed reliable.
The next problem encountered was where to place the thermal camera station. One idea was a tent, but it was early spring and still cold, so they found a suitable spot indoors. To complete the implementation, they only needed a six-foot table and a plexiglass shield.
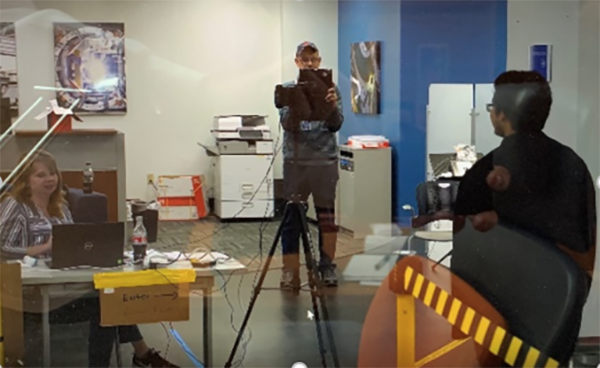
The thermal imaging process was implemented as a trial Sunday night March 29, then implemented at 12 sites throughout GEA. Each employee gets their thermal image read with a simple pass-fail test and two lanes: pass and go to your workplace; fail and follow an exit path.
Note: Two important points: 1) The system is not a medical screening. 2) To respect privacy, data on each individual is not logged.
Problem Three: Make assembly line work safe for social distancing
- Question: How to ensure assembly line workers maintain the 6-foot social distance, a problem with many tentacles?
- Thinking: Rebalance the line.
- Approach: Create new standardized work
Both GEA and HM ordinarily run fast Takt Times, even under 20 seconds, and produce similar-sized products, with the implications those facts have on the distance between workers and the challenge of respecting social distancing in those conditions.
The countermeasure: For the manual assembly line work, the line is slowed down, and stations are spaced out. For jobs that require workers to be less than two pitches from each other, place plexiglass barriers between workers that are closer than six feet.
HM’s approach:
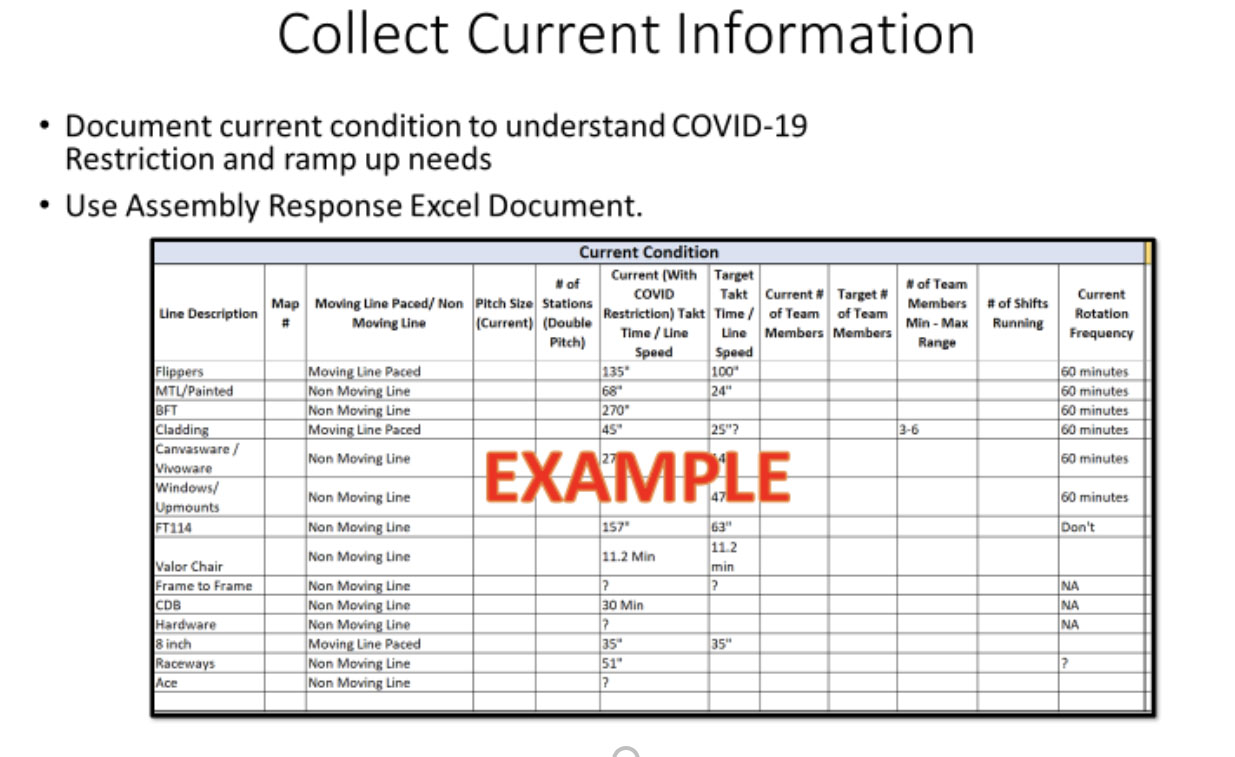

HM’s guidelines:
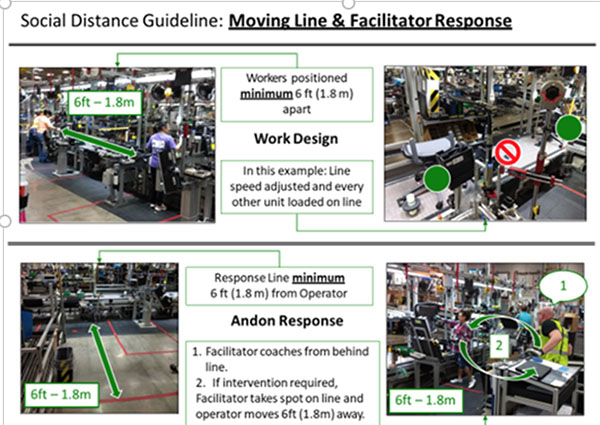
- Continue rotating job assignments but not at the standard rate. Instead, rotating once or twice a day, at most.
- Less frequent rotation is requiring us to reanalyze the actual work to eliminate the strain of difficult jobs. Before, for demanding jobs, we just rotated more and more frequently, so one worker wouldn’t have to bear a heavy burden for too long.
- Inserted a 30-minute gap between shifts for cleaning.
At GEA: Similar steps have been taken. Here’s a look at one of their many assembly lines with barriers placed between each operator.
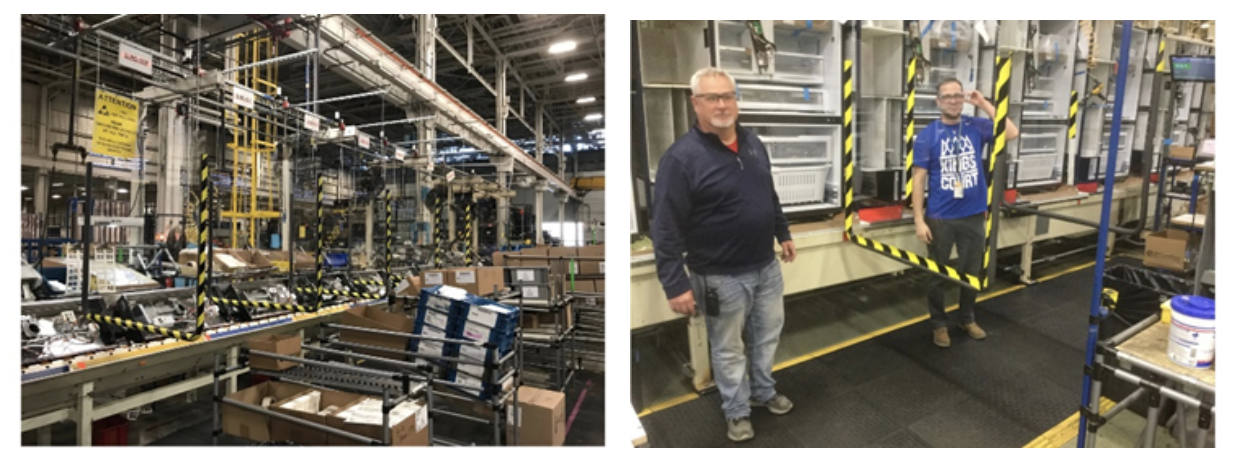
Problem Four: Maintain social distance for Team Leader Andon response
HM has developed new standard work for Team Leaders, who are trained to respond and step in quickly to help struggling Team Members; it is an essential and deeply held habit. The new standard is as follows:
- When TM calls, T/L responds but stands six-feet away from TM. If the operator’s problem is one of timing or something the TM can take care of by him or herself, the T/L allows the TM to take the time needed to sort it out.
- If the problem is something that requires T/L to step in, the TM steps aside, the T/L steps in and intervenes, then steps away, and the TM returns to the station.
- Markings on the floor indicate the six-foot distance, so T/Ls don’t get too close to TMs when answering Andon calls. (GEA is adopting this new standard work for Andon response.)
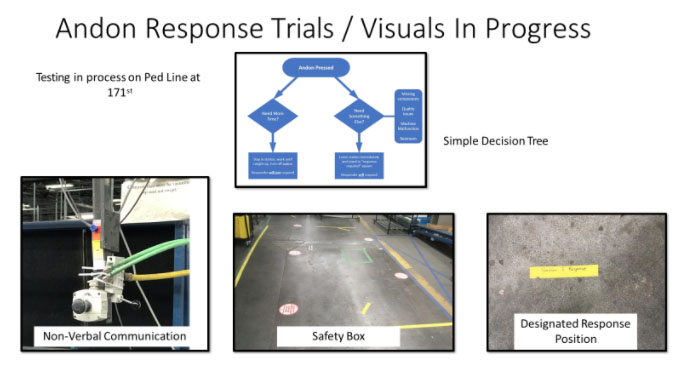
- Safety Box
- The designated response position for responder
- Entails enabling non-verbal communication
Problem Five: Apply social distancing to other, non-assembly line, work areas
HM: created “Guidelines for Non-moving Line Work,” to ensure social distancing as this work is performed; they include:
- Work stations have 6-foot distance around them clearly marked
- Job shop areas have 6-foot distance around them clearly marked
- Maintenance workers follow the same guidelines as the Andon response
- Visual aids maintain social distancing during team huddles:
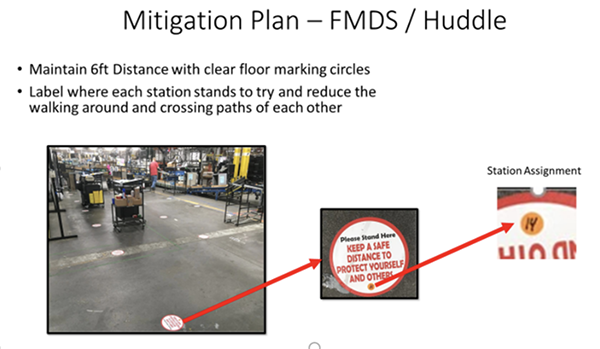
Note: When office workers return from working at home, they will follow similar guidelines and use similar visual aids.
GEA: Catherine Werner, the company’s Health, Safety & Environmental manager, found that (pleasant surprise!) the local Health Department has already issued some guidelines regarding the risk of different types of jobs. It describes the ranges of risk in a matrix: very high risk, high risk, medium risk, and low risk. Most GEA jobs are in the low-risk category.
Local OSHA visited and stated what they are seeing at GEA is best practice.
GE then:
- turned the guidance provided by OSHA in “Guidance on Preparing Workplaces for COVID-19” into a decision matrix that fits its situation (The OSHA guide mainly concerns with classifying jobs according to four levels of risk and specifying the associated PPE for each. In the OSHA guide, Very High Risk and High Risk refers to front line healthcare workers, and even Medium Risk refers to workers who interact directly with the public.)
- added guidelines about incidental passing to OSHA guidelines.
- conducted a job-by-job analysis to identify the jobs where people have to work within six feet of proximity all the time in their jobs.
- applied a hierarchy of controls for task-specific operations that require two people working within six feet of each other
- First, tried to design out the work that required close proximity
- If the work cannot design it out, tried to install a barrier or partition to separate employees,
- Finally, if social distancing (6 feet) or separation by barrier were not options, then employees were provided enhanced PPE (face shield and face mask). The enhanced PPE is additive to any PPE that is usually required to protect employees.
The decision matrix was helpful in both making the decisions about where to apply effort, but also gave workers a sense of comfort knowing that guidelines existed and were factored into the decisions.
Problem Six: How to handle the many other safety concerns that are cropping up?
1. Cleaning surfaces – when and how to clean
Additional effort was assigned to workstation cleanliness between employee changes and at the end of shift. A ten-minute cleaning time is required to optimize the efficacy of the cleaning product during breaks. Initially, GEA temporarily reduced worker job rotation. However, employees tend to like the rotation and have continued to reintegrate both rotation and additional cleaning by rotating on breaks and at lunch.
At one site, the T/Ls come in 15 minutes early to thoroughly clean workstations before the start of work.
Choosing the Right Cleaning product: The first selection criteria was availability. Many types were not available in the marketplace. GEA settled on an operating room grade cleaner, which is a spray-on-and-leave-on-style cleaner. It starts to disinfect in as soon as one minute and requires a dwell time of 10 minutes for full efficacy.
If GEA had had an unlimited product selection for cleaners, it likely would have selected a non-bleach wipe cleaner, which takes only 15 seconds to reduce the risk of Covid-19 effectively.The standard cleaners such as Lysol or Clorox non-bleach wipes are fast-acting (~15sec), so they might be better depending on the need for speed, for example, when jobs are rotated.
The cleaner selected by GEA is not suitable for food surfaces and not for porous surfaces such as cardboard.
2. Cleaning air – Ventilation
- Herman Miller has stopped all personal fans that blow horizontally. The company plans to evaluate, see, and test each fan to confirm where it blows before turning back on. It has not yet stopped vertical general ventilation fans.
- GEA also issued a recommendation to stop horizontal fans, and also is still using vertical fans. GEA HS&E is conducting a study with the University of Louisville to determine whether fans help or hurt in terms of dispersing harmful aerosols and droplets. It also is looking at overall building ventilation – working with facilities to make sure ventilation is working correctly.
- HM’s Matt Long: “Luckily, it’s still spring and not too hot yet. But it will get hot soon.”
3. PPE
At GEA: Team Leaders wear face shields. The company is making its own face shields with 3D printers at its makerspace, called FirstBuild, located on the campus of the University of Louisville.
Many small problems have cropped up. For example,
- The question to address: How to distribute masks to everyone, safely and efficiently?
- The first try was to place a big batch of masks in a heat shield bag
- Problem: People would grab a big handful, touching many masks in the process
- Countermeasure idea: Use a chute that distributes masks one or two at a time as the employee completes the scan
- Problem: How to replenish the stash of masks? Pull one-at-a-time is better than ordering big batches
- C/M idea: Kanban would work, but in this case need eKanban
- IT department contacted Wednesday
- By Thursday evening, had web-based eKanban replenish system for masks
- Ordinarily, it would have taken weeks!
GEA also placed Lexan barriers where they were needed.
Herman Miller will provide both a mask and a face shield to all members, starting distribution with T/L and maintenance and expanding from there. It, too, faced many barriers and followed the following sequence to address them:
- The first try was shrink-wrap – too flimsy and ineffective
- Then tried curtains (even shower curtains), which are better than shrink-wrap
- Now, moving steadily from non-fixed curtains to fixed
4. Incidental passing – water fountains, restrooms, hand sanitation stations
Maintaining social distancing in the restrooms and water fountains is an issue. To address this issue, GEA:
- Temporarily turned off water fountains per direction from the local Health Department, and provided alternate water sources
- Placed signs or barriers over the middle sinks in restrooms to facilitate social distancing
- Is moving to touchless restrooms and water fountains
- Designed and built automatic hand sanitizing stations, which reduce traffic to the restroom
- Added floor markings in all high queue areas – cafeteria, water fountains, restrooms, etc. Catherine noted that Americans normalize at a social distance of 3 to 4 feet. In some countries (GEA is international, including, of course, China), social distance norms are closer, so floor markings are necessary.
Miscellaneous lessons learned and observations so far
GEA: The area of first concern and the first scenario examined was the condition of the production employee. After working through those issues, we realized the supervisor – who passes through multiple work areas in the course of his or her work – was more exposed and more of a concern.
Other lessons
- Establish a Crisis Team and invite public health officials
- Name a Social Distancing Ambassador in every facility
- The work has:
- increased teamwork between lean team and HS&E team than ever before
- Increased cleaning in all facilities
- Communication is critical and has greatly increased
Herman Miller: Engineering design changes are moving very fast (GEA concurred)
Other lessons:
- Rotate at breaks instead of every hour or 30 minutes
- Create Andon response rules
- Maintain 6-foot distance between Huddles participants
- On the assembly line, ensure each job pitch is at least 6 feet away from another
- Skill using Standardized Work and balance chart tools is priceless
- Add additional PPE in the case of two- (or more) person jobs
- Add shifts where it makes sense
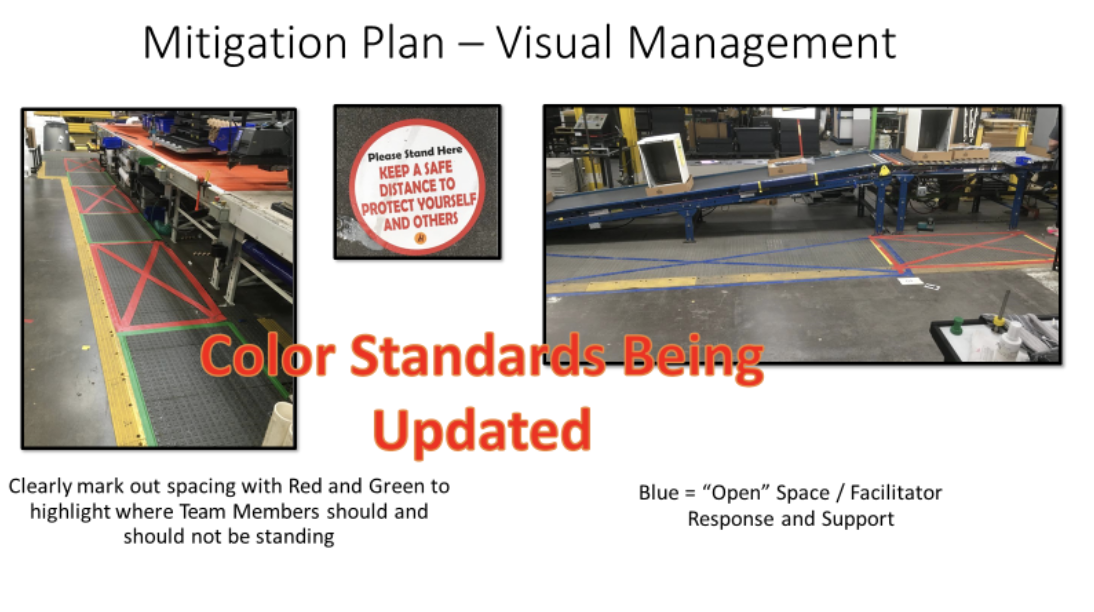
This is an incredibly interesting and thought-provoking article. As we begin to ease up on social distancing guidelines etc. what will the impact be on this kind of setup? Presumable rotation on work stations will be able to become more frequent? But in terms of social distancing markings etc. I presume it would still be equally as efficient to maintain them in situ?