Dear Gemba Coach,
I’m struggling to understand exactly what people mean by a “lean system”?
Understandable! “System” is one of these words, like culture, that has a meaning for every person who uses it, but none of these meanings are exactly the same – which is confusing. “System” in lean is used in many such different ways, and definitely the word can add to the confusion rather than clarify things.
Start with the official definition, and already, you’re in trouble? “System” has two basic meanings:
- A set of things working together as part of an interconnecting mechanism or network; a complex whole that is more than the sum of its parts.
- A set of principles or principles according to which something is done; an organized scheme or method.
Or, for systems thinkers, Donella Meadows’ definition:
A system* is an interconnected set of elements that is coherently organized in a way that achieves something. If you look at that definition closely for a minute, you can see that a system must consist of three kinds of things: elements, interconnections, and a function or purpose.
The earliest mention I’ve come across of “system” in lean is in Art Smalley’s translation from the Japanese of Taiichi Ohno’s preface to the first leaflet on the Toyota Production System: “TPS is a series of related activities aimed at the elimination of waste in order to reduce cost, improve quality, and improve productivity.”
This “system” has been interpreted in many different ways. In the early days of copying Toyota, automotive executives thought of the Toyota Production System as a set of manufacturing procedures to get higher performance. Their basic thinking was that if you copied what Toyota was doing, you’d get the same results. For instance, I vividly remember a plant that had been designed to mimic Toyota’s exacting standards with very little space for inventory and rework. Because the processes didn’t operate at the level of Toyota processes, products to be reworked overflowed everywhere and the whole thing was in shambles.
Very early on, the sensei warned us that the Toyota Production System was not the System of Production of Toyota (what?). In other words, copying the system of manufacturing techniques of one Toyota plant at a given time would maybe help us gain some catch-up knowledge, but no insight into the “system.”
Then Steven Spear and Kent Bowen wrote the very influential article “Decoding the DNA of the Toyota Production System” in which they proposed that TPS rested on a system of rules:
- Rule #1: All work shall be highly specified as to content, sequence, timing, and outcome
- Rule #2: Every customer-supplier connection must be direct, and there must be an unambiguous yes-or-no way to send requests and receive responses.
- Rule #3: The pathway for every product and service must be simple and direct.
- Rule #4: Any improvement must be made in accordance with the scientific method, under the guidance of a teacher, at the lowest possible level of the organization.[1]
Although a pretty apt description from the outside, this approach turned out rather unhelpful to reproduce Toyota thinking as it encouraged the mechanistic thinking of “rules” already strong in the western mindset, whereas Toyota kept expressing a far more “organic” vision of a “people thinking system.” According to veteran Toyota executives, TPS was really a method to make people think, not to bind them more severely with rules.
As the tools became more familiar, another interpretation emerged, which was one of a “management system,” a set of practices to follow with discipline. This version started with the “model cell” approach and how to spread the models cells across the whole enterprise by creating supporting “management standards.” Probably the best exponent of the management system approach is John Toussaint who practiced lean in hospitals, some of the largest structures you can think of. In his great book Management on the Mend, he outlines his idea of a management system:
- A model cell, to show the rest of the organization what can be done and spread the tools
- Organization-wide values and principles that will guide de work
- A central promotion office
- A frontline management system with leader standard work
- Spreading the work through the system
- Realigning the rest of the organization’s people, policies, and practices to support that work
This is also a very powerful approach, but again, it brings us back to a very mechanistic understanding of “system,” whereas Toyota, according to Professor Takeuchi, sees itself as a “green tomato,” always growing, never ripe.
The first time Dan Jones saw a full system outside of Toyota was in one of my father’s plants in the early 1990s. Freddy Ballé set up from scratch three large, full scale systems:
the Valeo Production System:
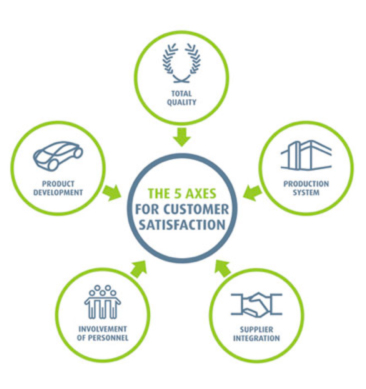
Then the Sommer-Allibert Excellence System:
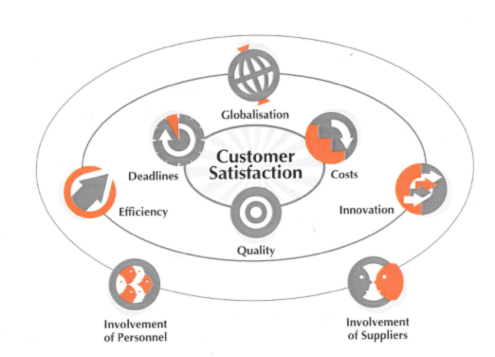
and then the Faurecia Excellence System (Faurecia acquired Sommer Allibert)
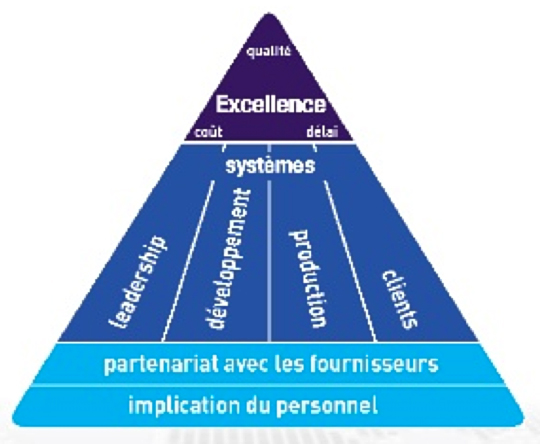
– Systems that continue to this day, decades later. What he had in mind in all three cases was outlining the key challenges the firm had to face. In many ways these “systems” fit the definition of a set of interrelated tools, like a management system
But what frustrates my father to this day is that this is not what he set out to do. Studying Toyota since 1975, and having had his own progressive “aha!” moments in Toyota plants and engineering offices, Freddy understand a system as a set of interrelated “typical problems/typical solutions.”
Every process has at least one large misconception that reduces its efficiency. In Valeo in the early days, the two largest misconceptions making production cells inefficient were:
- Manpower, Machine, Material, Method variations creating instability in the parts flow and making it impossible to level work for flow
- Large batches crowding the processes with inventories.
Freddy therefore spread “flow and layout workshops” through the plants along with SMED workshops. Plant managers and the central corporate teams did develop a set of procedures and practices to make the results stick. And this became a bureaucracy in itself.
One of the accidental outgrowths of the Valeo Production System experience is the ubiquitous “roadmap.” At one point, bewildered by all the various learning points they garnered from the collaboration with Toyota and frequent trips to Toyota suppliers in Japan, Freddy and a consultant came up with a two-dimensional way to describe progress:
- Maturity level from 0 = nothing to 5= excellence
- Lean topic by topic
The resulting roadmaps (entire folders of them) where fascinating to compile, as it structured the Valeo learning curve, but, to Freddy’s disappointment turned out rather useless to roll-out the transformation across plants. Learning, it turns out, is an individual experience and although executives can be guided by a sensei, there are no generic paths to learning. Learning remains completely situational, depending on the site conditions and the person’s path of “aha!” from practicing the various tools in their specific conditions. This, by the way, has not stopped endless companies to recreate roadmaps in order to steer their lean transformation (without success) and without ever recognizing they were just reinforcing the bureaucratic aspect of the “system” rather than encouraging the kaizen spirit.
Freddy always understood the need for a certain amount of bureaucracy to make these ideas stick – the bureaucracy we now call a “management system,” but he was ever so irritated by the many managers who would go through the motions without ever understanding the underlying need to address the “typical problems/ typical solutions” to gain performance by making work more effective.
So this would be my definition of a “lean system” – a set of typical problems/typical countermeasures which can be ritualized as “lean tools” but where everyone must look for the specific countermeasure in their own situation on their own gemba, to gain both performance and a deeper understanding of the endemic problem. The “system” part of it is that as you progress, you realize two things:
- Your list of typical problems increases one problem at a time, with a catalogue of specific countermeasures in different conditions.
- You start seeing how deeply interconnected these typical problems are as you work your way closer to the real root causes.
What of today? Of all the various attempts of creating a lean system, the best I know is John Bouthillon’s transformation of his construction company – described here in his own words . Bouthillon tackled one problem after the other, taking inspiration from the Toyota Production System to create tools for each of his team to explore the problem in every site:
Problem | Tool | Specific countermeasures | Principle |
Construction sites are dangerous, with high accident rate |
Safety daily barometer to distinguish good work habits from bad and 5S |
Each site has to focus on one bad work habit at a time and daily 5S |
Work safely, always |
Small mistakes create costly corrections and delays (which is costly) |
Daily problem solving analysis to learn to see problems correct now rather than continue working |
Problems are unique to every site and every day, each site has to focus on one problem, its cause and what countermeasures should be taken now. |
Right first time |
Each different trade works according to its own schedule, leaving many obstacles for the next person |
First day sheet: by checking the end of the first day to establish a clear improvement plan for the whole job, detailing how we want the job done in terms of scheduling and execution |
This requires each site management to delve deeply into trades work and understand what a fully completed job is, not starting many things and eventually finishing. |
Finished and gone |
When various different professions intervene, they each protect themselves against other’s inefficiency, creating more inefficiency |
High level plan to visualize key milestones and analyze weekly the impact of problems now on the overall lead-time of the project. Finish work before starting something else. |
Learning to turn adversaries into friends by creating in each sites a clear run for them to work – this is different from site to site |
Accelerate the flow of trades |
Construction uses many very traditional methods, several which have a high environmental footprint – whereas buildings have a high impact on total energy consumption |
6-step Toyota kaizen method to explore technical ideas to reduce footprint, as specific opportunities arise from building design |
According to construction choices, different sites offer different opportunities, some of them which can later be tried on other sites |
Lower the carbon footprint |
To conclude, there are indeed two aspects of a “lean system”:
- A method based on a set of principles: A clear list of interrelated (typical problems/typical countermeasures) in your own business to discover progressively – with their interactions. (For example, JIT aspects are linked to jidoka and vice versa, and both are linked to works standards and kaizen.)
- Working parts: The tools (standardized analysis methods) that will help local managers understand these typical problems in their own situation and look for specific answers to the typical countermeasure with their own staff – and how these tools fit together (for instance, never seek productivity improvement without quality, quality without lead-time and cost, etc.)
Human being are both always looking for innovative solutions (or at least new ways of doing things) and also, at the same time, always ritualizing whatever they do collectively. So yes, systems involve a certain amount of bureaucracy – tools, procedures, roles, etc. But the aim of a lean system is to keep people learning and thinking more deeply. Therefore you need to always keep an eye out for the bureaucracy winning and turning your system in ritualized activities that no longer deliver performance improvement and team engagement. There is no right balance other than to recall the senseis’ lesson that the aim of lean tools is to develop the kaizen spirit in every person everywhere, all the time to support dynamic gains – not to apply the lean tools to every process in the hope of optimizing operations.
[1] https://hbr.org/1999/09/decoding-the-dna-of-the-toyota-production-system