Whether it’s a pull-based inventory control system for keeping the pantry stocked, or using an A3 to help our kids learn how to solve problems, every lean thinker has had a moment when they’ve thought, “If I applied this concept to my daily work or at home, just think how much simpler and more efficient and less stressful everything would be!”
For more than a decade Jim Benson and Tonianne DeMaria Barry have been doing just that. Authors of the Shingo Award-winning book Personal Kanban: Mapping Work, Navigating Life, they help individuals and teams apply lean management principles to work, project and time management.
Benson comes from an agile software development background, which he characterizes as a batch and queue system for knowledge work. As a manager in the early 2000s, he was looking for other ways to manage such tasks and happened upon kanban concepts, which he first adapted and applied to his development teams, then later to managing individual work.
“Kanban does two things, it makes what’s going through a processing system visible, and it limits the number of things that can be produced at any given point in time,” says Benson. “That forces people to pay attention to what’s being done.”
We mistakenly believe that knowledge work is unmanageable, he adds, because it’s invisible. But the practical problems that managers are continually trying to solve are universal: How do I prioritize my work? How do I know what other people are doing? How do I know when to collaborate? How do I know which tasks to delegate?
Addressing these questions requires the right information to be available when it’s needed so that people can make good decisions. The two rules of personal kanban enable this information transfer:
1) Make your work visible because you can’t manage what you can’t see, and
2) Limit your work in process because you can’t do more work than you can handle.
Why “To Do” Fails
Knowledge workers often take on too much because they can’t see all of their work, and because they confuse capacity with throughput. To explain the difference Benson and Barry offer the analogy of a freeway. A freeway reaches maximum throughput at somewhere around 65% of capacity, and is a parking lot at 100%. To actually get things accomplished, work needs to flow, not be stuck in gridlock.
That’s why maximizing capacity (personal productivity) by filling every spare minute of time sacrifices quality (effectiveness). When we try to do too much, nothing gets done or it doesn’t get done well. Limiting work in process (WIP) also discourages multitasking, which researchers have repeatedly found to be counterproductive.
Applying a kanban approach to knowledge work enables an individual, team, group or company to see the work that they have to do, understand the work that they are doing, and appreciate the work that they’ve completed. It takes very little time to setup. The authors recommend using a whiteboard because it’s easy to adjust as your understanding of team and individual value streams deepens.
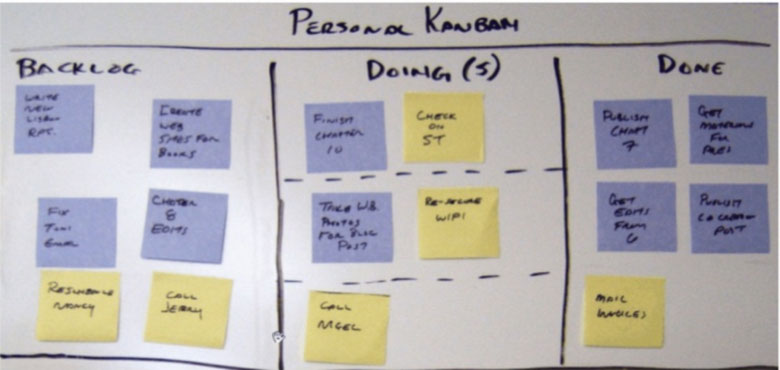
A long section of Personal Kanban is dedicated to the evils that to-do lists inflict on us. The primary failure of to-do lists is that they don’t provide context. Without context we approach tasks in a reactive or fire-fighting mode. What’s the biggest emergency now? As long-time lean thinkers will relate to, reaction isn’t prioritization. The personal kanban approach creates context and clarifies the causal relationships between tasks.
Like other visual management tools, personal kanban is relatively straightforward to implement because there isn’t a rote, external process that needs to be adopted and enforced. The immediate objective is simply to make the work that you’re already doing visible, which immediately presents opportunities for improvement and the impetus to do so.
“When we can’t see a problem, we tend to complain about it,” he says. “When we can see it, it drives us nuts and we have to fix it.”
Very true 🙂 If you want to learn even more about personal kanban boards, this article might be worth reading: https://kanbantool.com/kanban-guide/personal-kanban