Editor’s Note: This article, updated in March 2022, is the first of 3 focused on exploring the crucial role standardized work plays in a lean enterprise. Read the first and second in the series.
In the last two columns, I introduced five neglected aspects of standardized work. In response, several people requested a column on what, exactly, standardized is. So here’s a brief introductory outline, following LEI’s Three P framework of Purpose, Process, and People. Incorporate these things when setting about to establish standardized work.
How Standardized Work Serves Your Purpose, Process, and People
Purpose
- Establishes a baseline for improvement.
- Creates a means of realizing attainment of organizational goals at the front lines, where the organization’s real work takes place.
- Serves as a means of engaging the people who do the work, enabling you to encourage the desired level of engagement required of the worker. (In other words, remember why you want to establish standardized work.):
- Commitment, not compliance
- Improvement, not steady-state — There is no steady-state!
- Creativity, innovation, problem-solving — Improvement of the standardized work
- Initiative, not merely following orders
- Builds from work standards.
- Ensures safety, quality, performance.
- Enables observation and process study.
- Includes three Basic Standardized Work Elements:
- Takt Time and cycle time (TT vs. C/T): In other words, timing — the timing demanded by your customer and the timing constraints of your processing capability
- Sequence (including layout and man-machine combination with process capacity sheets and standardized work combination table): In other words, determining the optimum order of producing the product or service — first do A, then B, then C.
- S-WIP: In other words, the amount of in-process “stuff” that is required, no more, no less. That stuff may be material, parts, or information.
- Establishes a standard process for making changes (i.e., Suggestion System)
People
- Offers a means of engagement, involvement, ownership
- Views each worker as an entrepreneur
- Incorporates Quality Control and Six Sigma
- Forms basis for training
- TWI – Training Within Industry
- If you don’t know about this program, learn about it!
- Job Instruction (JI), Job Methods (JM), Job Relations (JR)
(In Toyota’s case, standardized work and kaizen training has replaced JM, but companies would be well-advised to consider starting with JM, then consider Toyota-style standardized work later.)
- Skills Matrix – A plan for every person!
- Practice, practice, practice
- TWI – Training Within Industry
- Includes standardized work for non-standard work
- Three levels of standardized work
- Level 1 – doing repetitive production-type work
- Level 2 – supporting repetitive work
- Level 3 – doing knowledge-based or project-based work
- Standardized work kaizen for creative or knowledge work
- PDCA (Lean Product and Process Development by Al Ward)
- Three levels of standardized work
- Requires coaching, questioning (right questions), not telling, and making people think and take responsibility
- Assigns greater and greater responsibility to the operator
The Standardized Work Equation
And remember: The technical/process and the socio/people sides of the standardized work equation are equally important. Well-designed standardized work represents the technical and human dimensions of the work in equal measure.
The example of assembly-line standardized work described in Lean Lexicon, Fifth Edition, and Kaizen Express, which describes Toyota’s Fixed-Position Stop System, is a perfect illustration of these socio-technical components of standardized work:
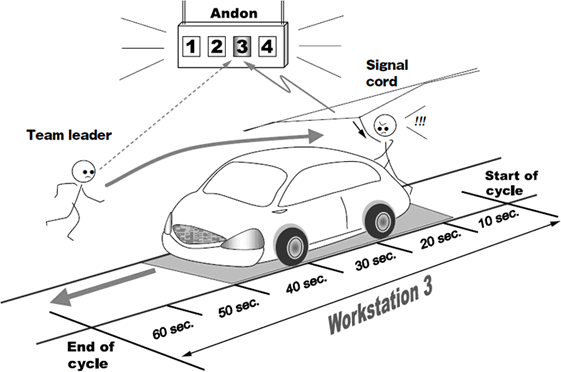
Fixed-Position Stop System
A method of addressing problems on assembly lines by stopping the line at the end of the work cycle — that is, at a fixed position — if a problem is detected that cannot be solved during the work cycle.
In the fixed-position stop system, an operator discovering a problem with parts, tools, materials supply, safety conditions, etc., pulls a rope or pushes a button to signal the supervisor. The supervisor assesses the situation and determines if the problem can be fixed before the end of the current work cycle. If the problem can be fixed, the supervisor resets the signal system so the line doesn’t stop. If the problem can’t be corrected within the remainder of the cycle time, the line stops at the end of the work cycle.
The fixed-position stop system was pioneered by Toyota to solve three problems:
- The reluctance of production associates to pull the signal cord if the entire line would be stopped immediately.
- Unnecessary line stoppages to deal with minor problems that could be resolved within one work cycle.
- The need to stop the line at the end of a work cycle rather than mid-way through the cycle to avoid the confusion — plus the quality and safety problems — inherent in restarting work tasks part of the way through a cycle.
The fixed-position stop system is a method of jidoka, or building in quality, on manual processes along moving assembly lines.
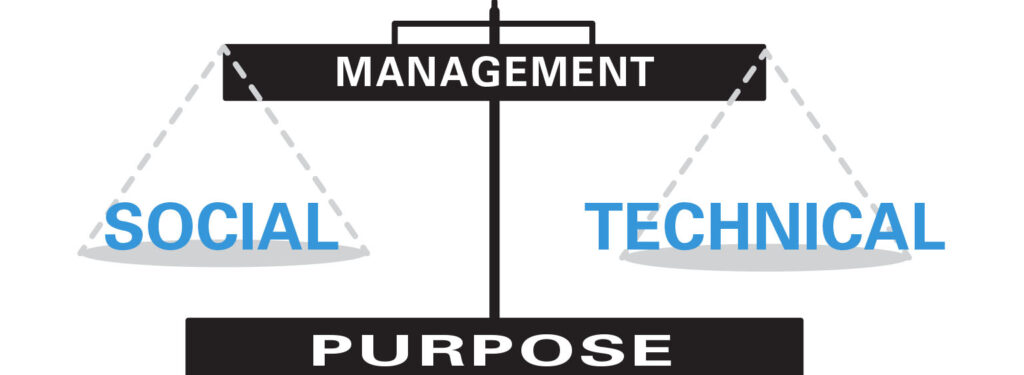
Look at your standardized work and structured improvement process (kaizen) — that is where you will find your culture!
Intro to Lean Thinking & Practice
An introduction to the essential concepts of lean thinking and practice.
Our production can be difficult due the nature of the components we work with and product we manufacture. It is not uncommon for the parts to fluctuate during a production run. The materials we work with are usually not the same, even during a solid run. The supervisors need to be capable of recognizing this and instructing the employees how to deal with these inconsistencies, as they are pretty much unavoidable in our type of manufacturing.