LAX aircraft maintenance facility reaps big returns in short time By Doug Bartholomew If ever there were a testimony to the flexibility of lean practices, it’s the FedEx Express Aircraft Maintenance facility at Los Angeles International Airport (LAX).
One of three large aircraft maintenance facilities in the Aircraft Operations Division of FedEx Express, the LAX hangar differs from a traditional manufacturing plant in one significant way: rather than assembling products, the facility performs both routine maintenance and safety checks as well as unscheduled repairs, both major and minor. Despite this variability, FedEx LAX has applied lean principles with impressive results.
Although FedEx Express operates about 170 aircraft maintenance facilities worldwide, including about 100 in the U.S. that perform routine maintenance that generally takes a day or less, it’s in this sprawling 950,000-square-foot facility — staffed with 550 employees — that the company performs much of its major service, repairs, overhauls, and equipment upgrades. “We do a lot of unscheduled work,” says Hector Chavez Jr., aircraft maintenance manager and a leader of the hangar’s lean initiative. In other words, the FedEx Express LAX staff must be prepared to replace or repair everything from a cracked engine nacelle to a faulty hydraulic line on any of the corporation’s 360 large cargo transport aircraft.
FedEx Express LAX’s lean initiative, which has been under way since December 2007, dovetails nicely with the corporation’s current emphasis on finding ways to reduce costs and boost revenues during the global economic downturn. To that end, the LAX facility has accelerated the aircraft upgrade programs it already had under way that are designed to reduce maintenance costs by increasing capacity with the same equipment and staff. “Here we have found opportunities where we can create capacity by using lean,” says Phillip Coley, managing director of aircraft maintenance at FedEx Express, who is in charge of the LAX maintenance facility as well as one in Indianapolis.
Fighting the Recession
To be sure, lean is paying off for FedEx Express at its LAX hangar. For example, take the facility’s bread and butter maintenance and repair exercise, the labor-intensive operation it calls a C-check — a series of deep maintenance inspections and repairs on an aircraft that typically took six weeks or so. Two years ago, with the same size staff, equipment, and floor space, the facility performed 14 C-checks. This year (April 2009) LAX has already done the equivalent of the current fiscal year’s as well as next fiscal year’s C-checks. This year the facility plans to complete 30. The C-check improvement alone is especially critical to the company, because FedEx Express’ Los Angeles Airport operation is the only maintenance site handling this major maintenance regimen. Any overflow of C-checks FedEx LAX can’t handle are outsourced at an average cost of about $2 million excluding parts. “Lean has enabled us to optimize our resources,” Coley says. In other words, any work that can be brought back in-house yields immediate and significant savings. FedEx Express delivers about 3.4 million packages and 11 million pounds of freight each day worldwide. The largest operating company in the $38 billion FedEx enterprise, FedEx Express brings in the lion’s share of the revenue– $24.4 billion in fiscal 2008. While saving a million dollars here and a million there may not seem like a lot, Coley says every bit of savings counts dearly during the downturn, which has resulted in a decline in FedEx’s package delivery and cargo business. The company’s domestic package volume when measured year-to-year was down 7.7 percent as of the second quarter of its fiscal year ended last November 30, and international priority package volume was off 6.7 percent over the same period year-to-year. Ground volume (-0.9 percent) and freight shipments (-2.0 percent) were down as well. To reduce costs, FedEx Express plans to park some airplanes that are not being fully utilized for possible use later at a site near Victorville, CA. In the near term, other aircraft, including nine aging 727-200s, are being permanently retired. Ten leased A310-200s also are being returned.
“C” Check Savings
Despite the business slowdown, the FedEx Express LAX staff of lean-trained aircraft maintenance technicians is digging in for the long haul, finding ways to save money for the company until better times return. A key piece of the strategy is to continue the hunt for lean opportunities to remove waste and refine maintenance operations for greater efficiency. In fact, a radically redesigned approach to the way the LAX facility handles the all-important, labor-and-parts-intensive C-check of a jet aircraft has already yielded FedEx some big dividends. By reducing the typical time it takes to do a C-check from 32,715 man-hours six months ago to 21,535 man-hours today, the facility is able to handle more work (see chart below). That translates into a savings of $2 million, excluding parts, per C-check that otherwise would have had to be performed by a paid third-party aircraft maintenance firm.
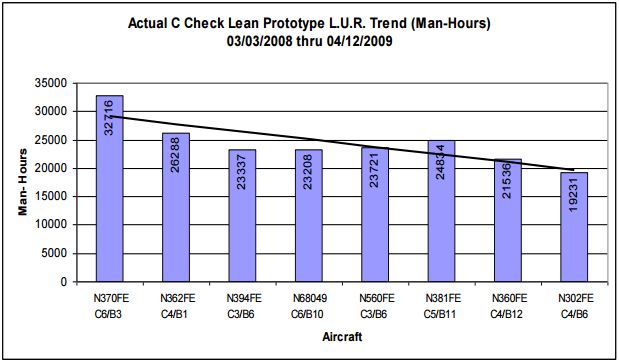
Some typical C-check activities the mechanics perform include overhauling the aircraft’s cargo loading system, overhauling the cockpit seats in some planes, and overhauling the aircraft’s large flaps, the adjustable rear portion of the main wings that is critical for creating lift on takeoff and drag on landing. FedEx LAX has already done initial kaizen on the cargo loading system maintenance, reducing the time that process requires from about 30 days two years ago to about 18 to 20 days now. Additional C-check refinements include further improving the flap overhaul/replacement process, and improving the kitting system to speed the cargo loading maintenance process even more. Through these more efficient C-checks, as well as a critical landing gear modification and other lean initiatives, FedEx LAX and its sister facilities in Memphis and Indianapolis, are expected to save the company an estimated $18 million during the current fiscal year.
Maintenance facilities at Memphis and Indianapolis handle the “B”-check maintenance procedures that typically require about 400 man hours or more. Lean is paying off considerably for these facilities as well. As an example, Indianapolis has cut the time it takes an out-of-service aircraft to receive a B-check service from 60 elapsed hours to 30 hours, with a June 2009 goal of further reducing the B-check time to 24 hours. Reducing the elapsed hours by half on a B-check allows more hangar capacity, which allows the facilities to handle more special visits and aircraft modifications. In Memphis, for instance, increased capacity has been used to handle extra work such as installation of fire suppression systems and HUD (Head Up Display, which allows pilots to see cockpit data without looking down, similar to the system military fighters use). In the past, these modifications would have been sent to outside contractors. By performing them in-house, FedEx Express is able to save on external spend.
Value-Stream Mapping Coley points out that FedEx Express’ use of the C- and B- checks to designate certain levels of maintenance programs and inspections are not standard industrywide, generic terms, rather they are customized FedEx terms only. “A C-check might be anything at a different airline, depending on the approved maintenance program and operational pull,” he explains.
Excluding unexpected major repairs, most C-check maintenance operations are fairly predictable, requiring certain new parts and specific tools the aircraft mechanic technicians need to install them. Using value-stream mapping, the lean teams analyzed all the standard work involved in a series of prototype “vanilla” C-check. They came up with 68 milestones, or key aspects of the overall process.
Then they were able to sit down and plan each C-check, breaking it down into four-hour increments. By understanding each four-hour block of mechanics’ time, Coley explains, “They learned how to pass the baton without dropping it, so that one mechanic can pick up on a task exactly where his predecessor on the last shift left off.” The end result was that they were able to carve plenty of wasted time and movement from the various processes that make up the typical activities in a C-check. For example, a couple of big bottlenecks were eliminated by finding ways to place pallets of special tools and airplane parts right on the hangar floor where the airplane maintenance technicians (AMTs) are working. Before the lean initiative, mechanics typically queued up in front of the parts stock room, often waiting for 15 minutes or longer, just to get batch of screws or a particular component. With some of the best-paid airplane mechanics in the industry on staff, that waiting time can be costly.
Both the parts staff and the AMTs participated in figuring out which parts were most likely to be needed during the C-check operations. They also decide the best way for the highest-use parts to be displayed on a “roto-bin,” a cart with a parts rack, and brought to the location closest to where they’re needed, thus eliminating unnecessary walking for mechanics. They even found a way to place a “quick parts” box on a level with the cockpit/nose of the aircraft for mechanics working on that part of the plane. “The difference in the way the AMTs work now has been easily 180 degrees,” Chavez says. Instead of taking up to four hours for setup, it now takes two hours or less. “Now our mechanics have the parts they need just 10 feet away. They need air, a ladder, electrical — it’s all just 10 feet away.” For less commonly needed parts, the facility has located four terminals on the floor where mechanics can look up the specific parts they need. Similarly, when the AMTs found they needed a special tool, such as a four-foot-long torque wrench, they had to go to the tool crib and — you guessed it — line up once more. Again, FedEx LAX engaged both the parts staff and the airplane mechanics in the kaizen to figure out the best sets of tools the AMTs needed close at hand for each particular repair or maintenance operation in the C-check. “We have a toolkit assigned to each mechanic’s task so we don’t have skilled people standing in line,” Coley says. “We realized that our internal customer is our mechanic.”
Speaking of tools, each airplane mechanic has his own full-size, multiple-drawer toolbox on wheels similar to those used by automotive mechanics. Before the LAX facility performed a 5S operation to clean up the workplace, these large wheeled toolboxes were scattered around on the floor, making it difficult for the mechanics to find their own boxes, let alone walk among them. Today, the boxes are lined up in neat rows, each parked in its own assigned location, allowing easy access for the AMTs to walk between them.
See examples of 5S improvements by FedEx LAX employees:
- Improved storage of panels and carts
- Carts for sheet metal and cockpit windows
- A tool to help check thrust reversers
- Improved sharpening tool
Brake Mods Pay Off
Among the most significant cost-saving measures the FedEx LAX facility has pursued aggressively during the downturn is its accelerated schedule for converting old steel brakes on aircraft to carbon brakes, which are more durable and require less frequent replacement.
Based on the FedEx LAX facility’s repair records on brake replacement, steel brakes last at most 337 cycles — with most aircraft flying two cycles, or round trips, daily — or about six months. By contrast, the carbon brakes provide 2,200 cycles of service, or about three years. With 8 to 10 brakes per airplane, the savings add up fast. The brake modifications save the company about $1 million per year in fewer parts and reduced labor cost per aircraft. The task of swapping out the old steel brakes for new carbon ones — a more complicated process than simply changing a pair of brake shoes as one would on a car — was so important that Coley and his team performed a kaizen exercise to find and implement ways to improve and speed the changeover. The result was that FedEx LAX got the time it took to do a brake modification down from about 15 days to 7 days. Another kaizen on replacing landing gear — there are four per aircraft — yielded a time reduction from 11 to 12 days down to about 5.5 days, Coley says.
Motivating Employees
Of course, getting airplane mechanical technicians, parts specialists, and other staff on the hangar floor to think lean wasn’t easy, Coley admits. “We invested a lot of lean training in our employees, because we believe that, ultimately, everybody should get to be a change agent.” Coley, who successfully re-energized a lean initiative at United Airlines in San Francisco, where he was director of airframe maintenance, knows that any lean program can be only as good as the workers who participate in it and believe in its success. To that end, he devotes a big chunk of his time to motivating employees and finding ways to bolster their commitment to the lean efforts. “It’s a major cultural change, to get people to do things because they want to do them,” he says. Chavez agrees, pointing out that when the lean program was launched, people were somewhat skeptical. “At first it was an uphill battle,” he says. “There was an attitude, ‘We’ve seen many of these programs before.’ It took about four months for people here to really understand this was going to be a complete change in the way business would be conducted. Now, it has really taken off.”
Coley likes to use visual tools to help motivate workers. He shows employees videos that demonstrate how lean works and show how it can pay off. He even takes groups bowling, assigning them to teams that compete with one another to see which is best at “balancing the workload” — i.e., finding the best combination of bowlers to achieve the highest score within certain parameters. “They actually start to collaborate to try to get the highest team score,” Coley says. “At the end, we do some lean training, and you can see they understand the concepts and how it works.” (The company also developed a group exercise program to cut injuries. Use this link to see pictures of the warm-up routine.) Besides using videos, he has lined the hallways of the office area of the hangar building with large color blow-up photographs of outstanding employees on the job. “I’m a believer that recognition for employees is effective,” Coley says. What’s different in this case, though, is that each month the workers are asked to choose an employee-of-the-month, instead of management (Coley or a manager) making the selection.
The LAX hangar received close to 1,000 suggestions in the past year. If a mechanic has an idea to improve a process, he can present it as a suggestion to the lean committee. “If it’s only something that takes an hour or two to do, we tell them they should just do it,” Coley says. Having the airplane mechanics and other hangar staff consider each suggestion and work out their own solutions to the way work is handled goes a long way toward making the lean program at FedEx LAX a success, Chavez believes. “The very way you present it to people is key to getting their buy-in,” he says. “We actually have the personnel who are part of the process help figure out the solution.” Adds lead mechanic Monte Petry, “One of the things we’ve learned here is that you’ve got to take everybody’s opinion into account before making a decision.” As a former airplane mechanic himself, Coley doesn’t put much stock in formalities. When he took the job a year ago, one of the first things he did was get rid of the personalized parking space for the director. In a similar vein, he spends a minimum of five hours a week roaming the work areas, including the hanger floor, the parts warehouse, and the tool storage area. “The mechanics know I’m out there on the floor to help them, do an independent audit, and that I have a check list,” he says. “I look to see if the leaders and technicians are active. Are the manager and lead mechanic touring the work area? My goal is to be on the floor three times a week.”
Box Score for Aircraft Maintenance C-Checks at FedEx LAX Before Lean Improvements:
- Actual wrench time varied greatly depending on the task
- Airplane maintenance technicians (AMTs) spent between 1.3 and 2.4 hours a day walking to get parts, tools, etc.
- AMTs made 106 trips (five trips per mechanic) in pursuit of expendables and consumables
After Lean Improvements:
- Wrench time improved and moved toward a standard that the Lead Mechanic could predict
- AMTs spent between .47 and 1.3 hours each day walking to get things other than consumables and expendables
- AMTs made approximately 25 trips to obtain items for tasks during observations (carbon brake mod, outside kitting, and point-of-use scope)
For More Information
FedEx Express — Founded in 1971 as Federal Express Corporation, FedEx Express is the world’s largest express transportation company, providing service to every U.S.
address and to more than 220 countries and territories. The company uses a global air-and-ground network to speed delivery of time-sensitive shipments, usually in one to two business days.