Learning lean thinking and practices has always featured a component of collaboration between organizations. We are sharing one approach used at LEI to help organizations accelerate their lean learning while assisting them in their efforts to improve. Periodically, we will share other key learnings from the CSTs with the LEI Community in future articles.
Through the LEI Lean Product and Process Development (LPPD) Learning Group, non-competing organizations collaborate, experiment, and learn together to improve their product and process development systems and performance. A component of this Learning Group is collaborative study teams (CSTs). A CST is a group of individuals from different organizations who come together under the guidance of a senior LEI coach to investigate causes, propose solutions, run experiments, and share learning to address a common challenge they are facing in their organizations. Five organizations formed CSTs within their LPPD Learning Group from 2021 to 2023: Caterpillar, GE Appliances-A Haier Company, MillerKnoll, Pella, and TechnipFMC.
Forming Collaborative Teams
To facilitate collaborative learning, LEI LPPD Learning Group leaders and their coaches regularly meet to discuss business challenges and share effective product and process development practices. Through these conversations, they identify topics that the organizations want to spend more time studying. Then, they form CSTs to learn and experiment with various countermeasures for 9 to 12 months.
To launch a CST, the LEI coach and Learning Group leaders draft a “Charter A3” to define the scope and objectives of the study team. Then, each Learning Group partner selects two to three interested people who can contribute their time and knowledge to studying the topic to join the CST.
The CST starts with understanding each organization’s current state, including challenges and effective practices. Next, the members start running experiments to address specific organizational challenges. Throughout the study, each organization has coaching sessions with the LEI coach to support them.
The CST members have working group meetings among themselves and with the LEI coach for the study team on a regular cadence, typically every four to eight weeks, to learn together. During these working group meetings, the CST members share their learning.
Each team member also brings back what they have learned to their respective organizations, typically by first sharing with their LPPD steering committees (the leaders in their company who are involved in the LPPD implementation). Specific learnings are then disseminated through each organization’s learning networks as they see fit (e.g., lunch-and-learns, centers of excellence, tech clubs, town halls, etc.)
So, each learning group organization benefits not only from its studies but also from others’ studies.
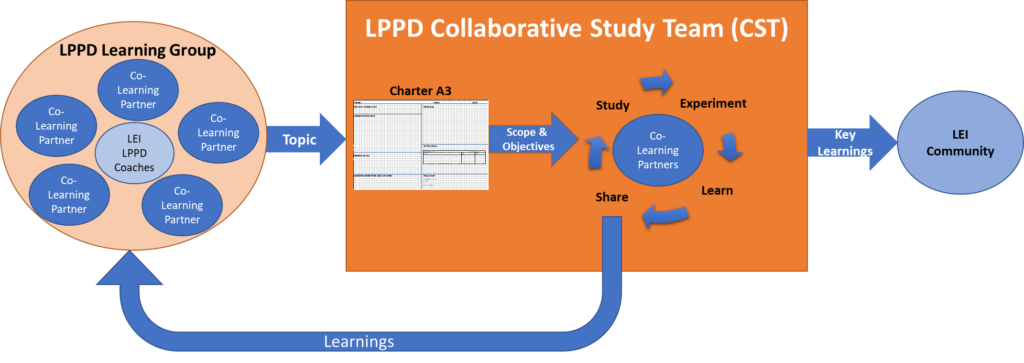
Making Design Reviews More Effective
Every organization engaged in developing products and services conducts design reviews as part of its process. Our colleague Jim Morgan refers to design reviews as the “crucible of innovation” and the “heartbeat of your development project.” The Learning Group partners unanimously agreed that design reviews are vital components of their development systems. However, they also felt they could improve the recipe for their design reviews.
In turn, they established a CST to investigate the key ingredients that would enable them to obtain more value from their design reviews. In this study team, the learning occurred in two stages. The first stage was each member sharing their organization’s current processes and practices for various types of design reviews. The team was pleasantly surprised that they could immediately adopt some best practices from the other companies.
The second stage involved running experiments to address common challenges they discovered after their first exchange. Of the many learnings that came out of the exchanges and experiments, some key ingredients emerged:
- Formal design reviews should bring cross-functional teams together to see the design from different perspectives. Everyone should contribute and be heard.
- For all types of reviews, decision rights should be clear (i.e., who is contributing, reviewing, and adjudicating the tradeoffs).
- Some structure enables better reviews, such as stating a clear purpose; providing data ahead of time to allow participants to think; focusing on the design, not the status, during the review; and applying checklists/standards to ensure nothing is missed.
- Peer reviews drive deep conversations and learning, making them the forum where people work together to solve problems. Some key ingredients include having a regular cadence; keeping the dialogue positive; challenging ideas, not people; and building a culture that is open-minded to listening and taking objective feedback.
- The design review outputs should be clear and documented, with the expectation that design review panelists will share the new knowledge with their respective organizations to enhance their checklists/standards.
- Everyone should develop skills to be good at giving feedback to encourage learning and not shutting down ideas, e.g., “That’s interesting. Have you considered…?, Here’s a suggestion…, I might be able to help you by….”
In our next LPPD post, we will share the highlights and results of two other successful LPPD Learning Group CSTs: Improving the Effectiveness of the Study Phase and Developing People and Their Technical Skills as They Develop Products.
Go to the Source:
To learn more about lean product and process development, connect with an LEI LPPD coach.
To stay connected with the LPPD community and learn more about what we are studying and learning, please subscribe to the Design Brief.
Designing the Future
An Introduction to Lean Product and Process Development.