Most traditional companies find lean nearly impossible to understand, let alone implement, because their leaders lack the “lean eyes” that come from the thinking that only occurs in someone deeply rooted in the lean fundamentals. These core ideas enable the lean manager or sensei to see things the traditional manager cannot and quickly grasp the opportunities. Further, they clarify the logic behind the necessary changes in a lean transformation and reveal the impact this conversion will have on the company’s customers and, ultimately, on its enterprise value.
Whenever I visit various companies to talk to their management teams or tour their facilities and give feedback, I always start by reviewing their annual report. The report provides a quick snapshot of how well they are doing and what I can expect to see. The balance sheet tells the most about how the company is being run and, most importantly, how management thinks. For example, companies that turn over their inventory only two to four times a year are clearly happy with wasting cash and floor space.
I then examine the P&L, focusing on margins. I know the margins that can be created with a solid lean implementation and can project those to forecast the opportunity here. Finally, I create a simple one-page analysis for the management team showing how much cash they could generate from various increases in gross margin and inventory turns. Most of the companies I visit are relatively large, so these opportunities are usually in the billions of dollars. Of course, they don’t always like being told this, but it helps them start to understand the opportunity.
Why is this so? Why can someone like me, who only sees things through the lens of the lean fundamentals, just walk in and do this? Because the traditionally run company is organized into a functional structure, by type of equipment in manufacturing or by specialty in service companies. As a result, the traditional company starts with enormous waste:
- 25% to 40% excess people
- 5x to 6x excess inventory
- 40% to 50% excess space
- 6- to 8-week lead times
- Persistent quality problems
Of course, the traditional management team cannot see any of this and denies that their company suffers these flaws. The lean manager, on the other hand, sees this instantly and knows that the only way to overcome these problems is by applying the lean fundamentals. So, let’s do that.
The 4 Lean Fundamentals
- Work to takt time
- One-piece flow
- Standard work
- Pull system
These principles sound simple enough, and in fact, they are. The problem is that none of them exist in traditionally managed companies. Which spells … opportunity. Let’s examine them one by one.
Work to Takt Time
Before any kaizen (improvement) work is done, the lean company asks, “What is the takt time?” This question puts the customer front and center in everything.
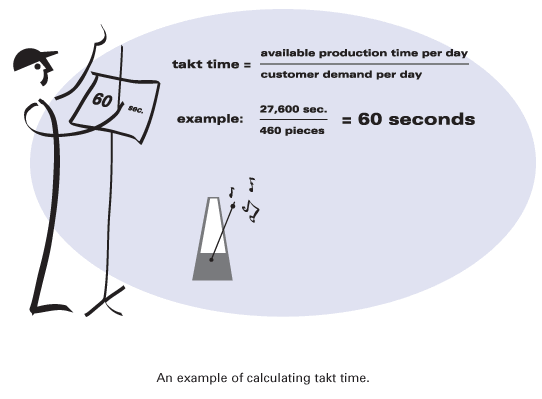
Takt time represents the rate of customer demand. Aligning this cadence to production links the customer directly to the work site and tells the operators what to make and when to make it — it provides the input to the lean ideal of “sell one, make one.” In many ways, this principle anchors lean practice: because excess inventory is the number one waste, it is essential to make what the customer wants, when they want it, and in just the amount they want. Working to takt time changes everything; it will reduce lead times from six to eight weeks to one to two days, which, in turn, will boost demand and enable gains in market share.
Traditional companies think about customer demand but not the way lean companies do. They start with a forecast of annual demand, not the hourly or daily demand that lean thinkers calibrate. They build everything according to this forecast, which prevents the factory from feeling real demand, separating the customer from the gemba (where the work takes place). They build in batches rather than units guided by actual orders and seek further gains by producing bigger batches. They replace the “sell one, make one” model with “sell one, make 10,000.” They carry excess inventory required for this approach and rationalize their six- to eight-week lead times as just the cost of doing business. And they lose business to the lean competitor who can deliver in one to two days at lower cost and higher quality.
One-Piece Flow
The traditional company’s functional structure forces it to build things in batches — the bigger, the better. These functional departments are often far away from each other, causing the product to travel long distances to get made. This work-in-process is stored along the way, resulting in the need for excess space and long lead times. This structure also requires a complicated management process to control everything — thus the use of sophisticated, i.e., expensive, MRP systems. Finally, the long six- to eight-week lead times make it very difficult to maintain quality: if you don’t discover the problem until six weeks after it happened, how do you get a permanent solution?
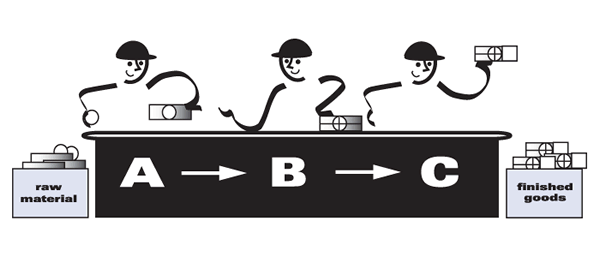
One-piece-flow cells shorten the time it takes to make something and reveal all the waste in the process, supporting continuous gains in productivity. One-piece flow is also the key to quality improvements: to make this work, you must have all the material, equipment, and people needed to make the product from raw material to packaging in a small space. If anything goes wrong, you can stop the line and correct it immediately — an immediate solution that I’ve seen will almost always result in a permanent fix. In my experience, just moving from batch to one-piece flow results in a roughly tenfold increase in quality. Also, you no longer need to produce according to a forecast because the customer demand can come directly to the cell as orders arrive throughout the day. You will still need to forecast capacity.
Standard Work
The traditional company calculates standard costs for every SKU out to four decimal places. These costs are based on a series of complicated assumptions, and, in most companies, the only people who believe they are accurate are the finance guys who created them. There is also a need to establish a standard that correlates to how long it will take to make a given product batch, as this information is needed to feed into the MRP system. Usually, these standards are set higher than necessary because some flexibility must be built in so that the MRP system can operate. In my experience, these standards are often way off from what is possible. On top of that, the focus is on making a number every shift. As a result, if you have ten people working on a shift doing the same thing, you will find that they each build the product in a slightly different way. The batch company is not concerned about this as long as they make the number. Also, in a traditional company, managers and engineers are responsible for setting the standards — and the standards rarely change.
Standard work for the lean company is entirely different. First, standard-setting is a step-by-step approach that details the tasks and amount of time it should take to do a given job. Everyone who does the job has to do it the same way. Otherwise, how can you have consistent quality or productivity? More importantly, the standard work should constantly change and improve as more waste is taken out of the system. In the lean company, this is the responsibility of the workers and their local supervisor, not some higher-level manager or engineer. That’s why the lean company is constantly improving where the traditional company is not.
Pull System
A functional organizational structure forces the traditional company to “push” production through its system. With six- to eight-week lead times to make a product, this becomes very complicated and causes numerous problems. It is not uncommon to create expediting departments to go in and find out where something is on the shop floor and push it through to meet customer demand, which complicates things even more as you have gone around your MRP system. In addition, there is no real connection between production and purchasing. Often purchasing is buying something that production is not planning to make and vice versa.
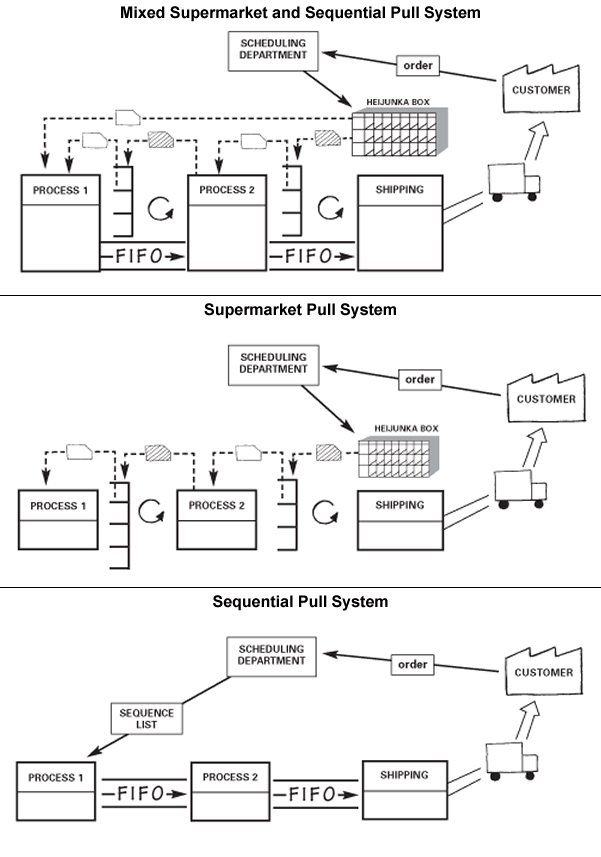
The lean company, on the other hand, has a pull system in place that links the customer to the factory floor and then directly to the raw material suppliers. Raw material and WIP inventory levels can drop from months to hours or a day or two. Raw material suppliers are expected to deliver daily or as close to that as possible. As a result, the factory can almost instantly respond to the customer without carrying massive inventory. Inventory turns can go from 3x to 20x, thus freeing up at least 50% of the floor space and lowering costs.It’s vital always to let these core ideas guide your turnaround.
Once you become a lean expert and understand the enormous potential impact of these lean fundamentals, you will be forever changed. You will look at a traditional batch operation and instantly see the possibilities for your customers, your market share, and, ultimately, your enterprise value. Give it a try!
Observation Skills
Learn to observe and understand work processes at the level of detail required to improve them.
Hi Art,
This article was very interesting and beneficial to me. I found your process of examining the annual report quite fascinating. I am curious though, after you do all these findings and present it to the management team they seem standoffish and in denial almost. How do you train a management to look to lean eyes and have this lean mindset?
Thanks Art. It would be good to see a similar article for a service / financial services organization.
inspiring, as alwaye, thank you Art for sharing this